3D Printing is a construction method using layers to create three-dimensional objects from a CAD model.[1] It is also known as additive manufacturing.
The technology has been around for decades within certain industries where industrial design patents, copyrights, and other legal regimes may apply. Click https://www.by3design.com/ to learn more.
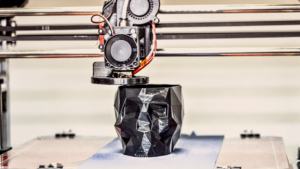
The rail industry, for example, has printed bespoke parts to restore old cars.
Rapid Prototyping
As an innovative tool that streamlines the path from idea to finished product, rapid prototyping allows engineers and designers to work more efficiently. This technology has impacted many industries and is becoming increasingly popular among consumers.
Rapid prototypes allow engineers to quickly evaluate the design of a new product, identifying any potential issues or flaws that may not be apparent through computer simulation or other methods. They can then make changes to the design before production begins, saving time and resources. This is especially helpful for products that require a complex geometrie or high level of detail.
The rapid prototyping process uses a computer-aided design (CAD) program to convert an original design into a digital file. These files contain three-dimensional data and can be printed using different methods. The earliest systems used stereolithography, which solidifies layers of an ultraviolet-sensitive liquid polymer. Since then, other types of 3D Printing have emerged, including fused deposition modeling, selective laser sintering, and laminated object manufacturing. Each method produces a different type of material and has its own strengths and weaknesses.
Once a prototype has been built, it is usually subjected to rigorous testing and evaluation to ensure that it meets all of the necessary specifications. This helps to identify any areas for improvement and ensure that the final product will be of high quality. Depending on the needs of a project, the prototype may also undergo post-processing techniques such as sanding or applying a protective coating.
Prototypes are often tested on actual users, who provide feedback that can be incorporated into the design to improve functionality and user experience. These tests can also reveal any problems with the physical structure or durability of a product, which can then be corrected before production starts.
Ideally, the final prototype should be identical to the product that will be manufactured in production, allowing for a seamless transition. This can be difficult, however, if the prototype is being produced through a traditional manufacturing process, such as injection molding or die casting. In this case, the prototype must be built with materials and dimensions that are compatible with these processes, which can add to the overall cost of the project.
Designing for 3D Printing
3D Printing is a process that turns digital files that contain three-dimensional data—created on a computer-aided design (CAD) or computer-aided manufacturing (CAM) program or from a 3D scanner—into physical objects. The printing machines lay down and fuse layers of material to create the final product. The process is called additive because it builds up the product by adding layers rather than cutting away or removing parts of the product as in traditional processes.
The resulting product is not as durable as traditional methods and can have visible layer lines, but it is very fast and cost-effective for prototyping and small batches of products. As the technology evolves, it will become more viable for producing larger quantities, but current 3D printers are best suited to prototyping and one-off production runs.
Designers use 3D printers to make prototypes and product models, and they are increasingly being used to produce final products. Some examples include shoes, furniture, tools and tripods, wax castings for jewelry, and gift and novelty items. Artists use them to fabricate sculptures. The technology is also useful for archeology and paleontology, with museums able to duplicate fragile artifacts that would otherwise be at risk of breaking during transport. Paleontologists can also reconstruct dinosaur skeletons and other fossils.
Because different materials have different properties—strength, flexibility, color, and surface finish, to name a few—designing for 3D Printing requires that the designer choose a suitable material before designing the model. Once the design is complete it must be “sliced” with specialized software, which converts the model into a series of layers that the printer will then build up from bottom to top. This slicing software also calculates the route the printer will take and provides instructions that are read by the machine to create the resulting object.
The democratization of the 3D printer—through affordable desktop machines that have sprung from the open source RepRap movement and inexpensive plastics like ABS and PLA—has made it possible for many more people to experiment with the technology. The ability to turn digital designs into physical objects has also transformed education, enabling students to design and construct anything from electric skateboards to prosthetic legs.
Preparing for 3D Printing
The process of 3D Printing starts with a virtual design of the object that is created using computer-aided design (CAD) software, a type of program used to create precise drawings and technical illustrations. The model is then prepared for Printing by slicing it into layers that the printer can print one at a time. This is accomplished using dedicated slicing software that converts the digital model into a series of instructions that are read by the 3D printer.
Once the sliced file is ready to be printed, it can be fed into the printer using USB, SD or Wi-Fi and the printing process begins. The slicing software also allows the user to change various parameters such as thickness of the layers or the speed at which they are printed, as well as the material that is being used. There are a number of different 3D printing materials to choose from, each offering unique qualities. For example, PLA is a low-cost option that is commonly used by beginners as it is derived from organic sources and offers great visual properties. However, it is not as durable or resistant to heat as some other options.
A growing number of people and businesses use 3D Printing to prototype new products and make small batches of finished goods. This type of manufacturing is known as rapid prototyping and it can be much faster and less expensive than traditional production methods such as injection molding. It also enables companies to keep production in-house, which can help protect intellectual property and maintain confidentiality.
Many of the skills that are being honed by individuals and businesses who use 3D Printing are similar to those needed in more traditional types of manufacturing. This includes problem-solving, iteration and attention to detail. It is also an excellent way to teach students science and technology, with progressive schools now offering hands-on STEM education through the use of 3D printers.
Other uses for 3D Printing include making end-use parts such as tools, jigs and fixtures as well as spare parts for machines. Car manufacturers have been leading the way in this area, with many using 3D printers to produce replacement parts that can be delivered to customers as soon as they are needed. This can greatly reduce inventory levels and production lead times.
Getting Started with 3D Printing
The ability to print physical objects is an exciting prospect, and one that is being utilized by a wide range of industries and individuals. From the medical field to the design industry, 3D Printing is a tool that offers an incredible amount of creativity and flexibility.
As you may have guessed from the name, 3D Printing is an additive process that builds up layers of material to create three-dimensional objects. This is a stark contrast to subtractive manufacturing processes like CNC or milling that cut, drill, and machine away materials to make the finished product. The beauty of this technology is that it offers the maker complete control over what is being made and allows them to use an endless variety of materials to make their final products.
To begin using a 3D printer, the first step is creating or downloading a 3D model of your desired object. These files are usually created through CAD software programs and are saved in a format known as STL (Standard Tessellation Language) or OBJ (OpenBOM). These file formats provide the printer with the information needed to build up the model layer by layer.
After the model has been modeled and sliced, it’s time to turn on the printer. The printer acts in a similar way to a traditional inkjet printer in that it dispenses wax- or plastic-like polymers onto the work surface in thin layers. After each layer is printed, the printer waits until it has dried completely before dispensing the next. This layering process continues until the object is fully built, making it possible to create intricate and detailed geometries that wouldn’t be possible with other printing methods.
While many people are using 3D Printing to create prototypes and models, there are many others who are using it to make actual finished products. Consumer products such as shoes, furniture, tools and jewelry can all be printed with a 3D printer. Even complex and specialized items like architectural models, medical tools and scale building replicas can be made with this technology.
In the medical field, surgeons are using 3D Printing to create surgical guides, orthopedic implants and prosthetics for patients. They have even been able to create patient-specific replicas of bones, organs and blood vessels with this technology. This is a significant development in an industry that relies on innovation to provide patients with the best care possible.